Replacing Mass with Science
Geosynthetic stabilization fabrics play a key role in achieving superior results with Ultra Base panels and are essential to "Replacing Mass with Science." These fabrics help stabilize soils without the need for stone or concrete and create the structural stability essential for success.
Popular Fabrics
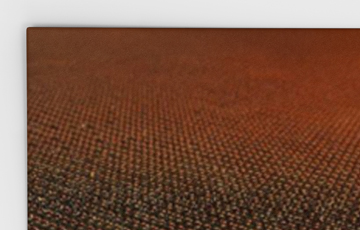
Mirafi RS280i
Woven, Permeable
This high-performance fabric offers a single solution for reinforcement and stabilization and is our most commonly used geotextile. Its high-modulus construction integrates key performance properties including soil reinforcement, confinement, separation, and filtration.
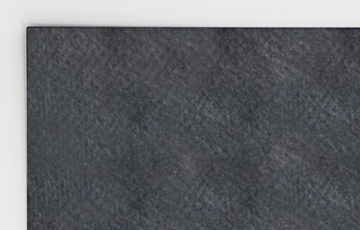
LM 800 NT
Non-Woven, Permeable
This felt like fabric is used primarily in court related projects where ball bounce is an important characteristic. It's almost always used with another supporting fabric as part of a 2-layer system and it eliminates dead spots by ensuring the cellular structure of the panel is completely supported.
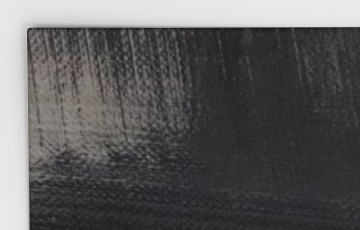
30 Mil
Woven, Impermeable
This woven impermeable membrane is used to control the flow of liquids. This fabric is a thermally welded polyethylene and is similar to a pond liner material. It’s often featured in rooftop projects requiring an impermeable layer or pet turf applications to prevent pet waste from penetrating the substrate.
Summary
The key to achieving superior results with UltraBase products is using the correct geosynthetic fabric for the application. The mission behind using UltraBase panels coupled with geosynthetic fabric is to “replace mass with science.” Our system provides drainage and structural integrity, reduces installation time and costs, and can even meet permeability restrictions—all without the use of stone or concrete.
Get Started with Ultra Base Today
Talk to an Ultra Base team member today to discuss your project, application, and pricing options. Our experienced team will ensure you're choosing the right Ultra Base product for your application.